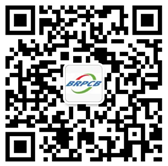
高频板涉及的技术相对较高,相关制作、检测设备和技术人员都是企业在跨越的一道难题,所以应充分考虑市场和技术、设备能力等方面的因素尤为重要。近年来,通信、汽车、基站、网络技术等领域的发展非常迅速,对印制板的需求发生了一些变化,大功率印制板、高频微波板的需求量增加。本文重点介绍高频板内层-压合层间控制和钻孔-电镀孔粗控制两个方式制作关键点,以供参考和建议。
高频板基本介绍
1. 高频板的定义
高频微波印制板是指用于高频率(频率大于300MHZ或波长小于1米)与微波(频率大于3GHZ或波长小于0.1米)领域的PCB,是在微波基材覆铜板上利用普通刚性印制板制造方法,部分工序采用特别处理而生产出的印制板
2. 高频板的应用范围
1) 移动通讯产品。
2) 功放、低噪声放大器等。
3) GSM.CDMA.3G智能天线。
4) 合入器、功分器、双工器、滤波器、耦合器等无源器件。
3. 高频板的材料特性
1) 介电常数DK比FR4板材要低(介电常数越低,它的电信号传播速度就越快)。FR4介电常数为:4.3,高频板一般在:2.0~10.0。
下表是某材料厂家的介电常数测试结果:
2) Tg温度比FR4高(Tg是指压合时玻璃化转化所需的温度)。Tg普通FR4:130℃,中/高TgFR4分别为:150℃/ 170℃ ,高频板一般为≥ 170℃
1.高频板工艺制作流程
1) 频段在<10Ghz的高频材料制作流程:
开料→内层→压合→钻孔→沉铜(高TG除胶流程)/板电→干膜→二铜→蚀刻→AOI检查→防焊→文字→成型→测试→终检→OPS→包装。
2) 频段在≥10Ghz的高频材料制作流程:
开料→内层→压合→钻孔→等离子处理→沉铜/板电→干膜→二铜→蚀刻→AOI检查→防焊→文字→成型→测试→终检→OPS→包装。
3) 小结:对比两种不同流程的差异在于,高频材料频段<10Ghz的材料采用高TG除胶方式,而≥10Ghz的则采用等离子除胶方式。以下为两种除胶方式的制作参数,以供参考。
4) 等离子处理参数如下:
5) 高TG除胶处理参数如下:(附注:等离子处理后需要通过滴水测试和水磨测试验证其效果)
2.重点工艺流程制作(附注:采用2次除胶方式,可通过镀铜后切片验证其效果)
1) 内层---压合层间对准度精度控制
① 内层菲林按照残铜率常规预补偿的方式,底片涨缩单层测三次元,涨缩均控制在±2mil以内。
② 压合熔合采用降低温度,加长时间的熔合方式,保证了各层间的熔合对准度。其条件、图片如下:
③ 通过多次压合试验确定压合程式参数:升温速率控制在1.5-2.3℃/min,高温高压时间150min确保料温达到180℃持续90分钟以上
④ 切片分析,层间偏移度要求≤4mil,实际切片测量层间对准度结果为75.788um(3mil),符合要求,切片图如下:
2) 钻孔---电镀孔粗品质控制
① 高频材料钻孔受其硬、脆等材料特性影响,钻孔优化的钻孔参数(高频板的钻孔参数表)
② 高频板建议使用精度较高的设备,采用1片1叠钻孔结构;选用不同孔径,不同钻咀类型,不同下钻次数,试验镀铜后孔粗品质对比(孔粗要求<1mil)。
③ 孔粗图片分析
全新钻刀500-800hit孔粗图片分析
④ 实验证实:通过电镀后切片分析,全新钻咀下钻500-800hit以及研一500hit、研二700hit能够满足孔壁孔粗品质要求,合格;其他条件均有超出1mil的现象,不合格。综合总体品质要求,建议钻孔采用全新钻咀,下钻次数控制在500-600hit镀铜后的品质较为佳。
结论
本文通过介绍两种不同频段的高频材料,总结出3-10Ghz和10Ghz以上的高频板的流程制作方式,通过试验跟进,得出以下结论。
1. 试验3-10Ghz高频板适合采用高TG除胶方式,10Ghz(含)以上的高频板适合做等离子除胶处理。
2. 通过分层菲林补偿和降低温度,延长时间热熔方式能有效控制层间精度。
3. 降低钻孔钻速、下刀速、起刀速和钻咀下钻次数均对高频板的孔粗控制有所改善。